Tasty source!
The Holy Grail for a lighting engineer is to create a unit that’s inexpensive to manufacture, low-cost to run, easy to direct and that produces light at a colour temperature that’s as close as possible to natural daylight. The human eye works best in daylight, so vehicle lighting that gets close to mimicking this is going to offer the safest and most effective option. This is why xenon lighting represented such a remarkable improvement over the halogen-powered systems that went before it.
Traditional, incandescent bulbs produce light with a colour temperature of about 2,700 degrees Kelvin (K), which is actually towards the yellow/orange end of the visible spectrum. A typical HID unit operates at 3,500K, which is a lot less yellow and much more neutral, while a modern LED can output light at 6,000K. This is a lot ‘cooler’ and more towards the blue portion of the spectrum.
I remember reading once that, as we age, the human eye becomes less and less sensitive to light at the yellow end of the spectrum which, of course, is exactly where most of the halogen-powered headlights sit. So, those of us of a certain age, who drive cars with traditional headlights, are actually bathing the nighttime road in a light that we find it increasingly difficult to see with!
Another interesting aspect which helped trigger the industry’s move away from HID lighting technology, is that the colour output from these lights varies during their service life. This will increase (becoming more blue), then peak and start to decrease again as the years pass. This typically occurs over a 3,000-hour period, but there are a lot of service-related variables involved, too.
Durability issues
When HID lights were first introduced, vehicle manufacturers proudly announced that these units would last the lifetime of the vehicle but, sadly, that hasn’t been the case. The life expectancy of xenon lights was relatively quickly modified to a more realistic five years and, most recently, research has revealed that it’s actually nearer three. The situation will be better with LED headlights as there’s no electrode consumption involved, so nothing to burn out.
Of course, there remain a great many cars around that still use conventional, filament-type headlight bulbs and, while most nowadays produce a reasonable output, bulb upgrades can represent an affordable and very worthwhile option. ‘High-power’ replacement bulbs from a quality producer will significantly boost light output to enhance nighttime driving and safety.
The genuine gains to be had nowadays from well-engineered, upgraded bulbs are very impressive. These used to be pegged to an improvement of about 30%, but the painstaking development work undertaken by specialist bulb producers like Ring means that it’s now possible to buy bulbs offering a genuine 150% more light output than the standard unit. What’s more, this has been achieved without affecting power consumption, so there are no potentially damaging, knock-on effects for the vehicle’s wiring, switches or sensitive engine management systems, as sometimes used to be the case. The only downside is a shorter service life but, the sort of performance gains now available easily outweigh this disadvantage.
As far as the automotive future is concerned, it would appear that the days of the filament bulb are numbered. The ‘solid state’ solution offered by LED technology will be progressively enhanced and, with unit costs being driven ever lower, the use of this lighting source is surely set to become increasingly widespread on vehicles of all types.
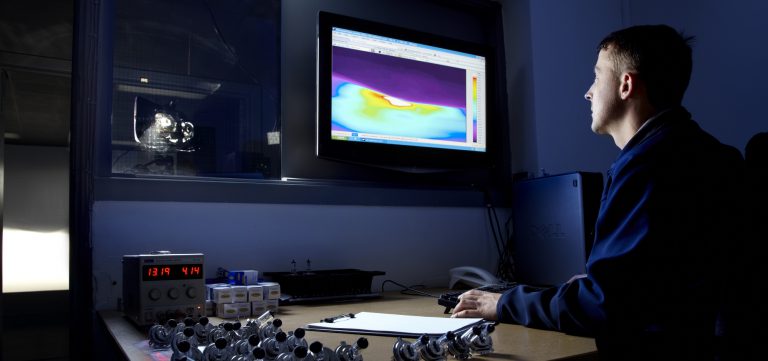
Light source development
Traditional bulbs operate by passing an electrical current through a thin wire, causing it to heat up and glow. The more current that’s passed, the hotter the wire gets and the brighter it glows. But there’s a balance to be struck. Overdo it and the filament will be consumed, the electrical circuit will be broken and the bulb will stop working.
The switch from conventional, filament-type light bulbs to halogen versions made a significant difference to light output. Greater brightness was achieved by ‘burning’ the filament hotter while controlling the greater evaporation rate of the filament by surrounding it with halogen gas.
When you see an old, filament-type bulb that’s failed, and you notice dark-coloured deposits on the inside of the bulb’s glass, that’s the residue from the burnt (evaporated) filament. Operating the filament in a halogen gas-rich environment triggers a reaction between the gas and the filament, causing the vapourised metallic particles to be re-deposited on the filament, thus extending service life.
High-performance halogen bulbs, which burn even hotter to achieve their greater light output, are able to do so because, as well as a halogen gas, the bulb also contains xenon. These gases are contained within the bulb’s glass envelope at a very high pressure, which acts to preserve the filament to an even greater degree.
Nevertheless, wire filaments remained an inherently weak link, with their gradual evaporation and vulnerability to vibration meaning that service life is always going to be limited. Removing the filament from the equation took vehicle lighting technology to the next level, with high intensity gas discharge (HID) and LED bulb types significantly boosting both light output and quality, as well as overall durability.
Light brightness is measured in units called lumens, and a conventional halogen bulb typically produces about 1,500 lumens. This compares to an HID bulb which outputs about 3,000 lumens while, somewhat surprisingly, the latest LED units are producing about 1,500 lumens. Arguably, they represent something of a backward step in output terms but, in every other respect – cost, efficiency, weight, electrical complexity, service life etc – they are superior.
Anecdotally, drivers are noticing the difference between HID and LED headlight systems, and not in a good way. However, it has to be said that the reduction in brightness is somewhat offset by the fact that LED light has a significantly higher colour temperature than HID light, so the illumination can appear more natural.
Unfortunately, thanks to the vagaries of the European type-approval system, LED lights have to be homologated as a single unit, in contrast to HID and halogen units, the components of which are homologated separately. Consequently, HID and halogen failures can be rectified with a replacement bulb (or other component) but, when an LED headlamp fails, the light unit has to be replaced in its entirety, which is massively more expensive.
Check out the latest in Ring's Performance Bulb range below: